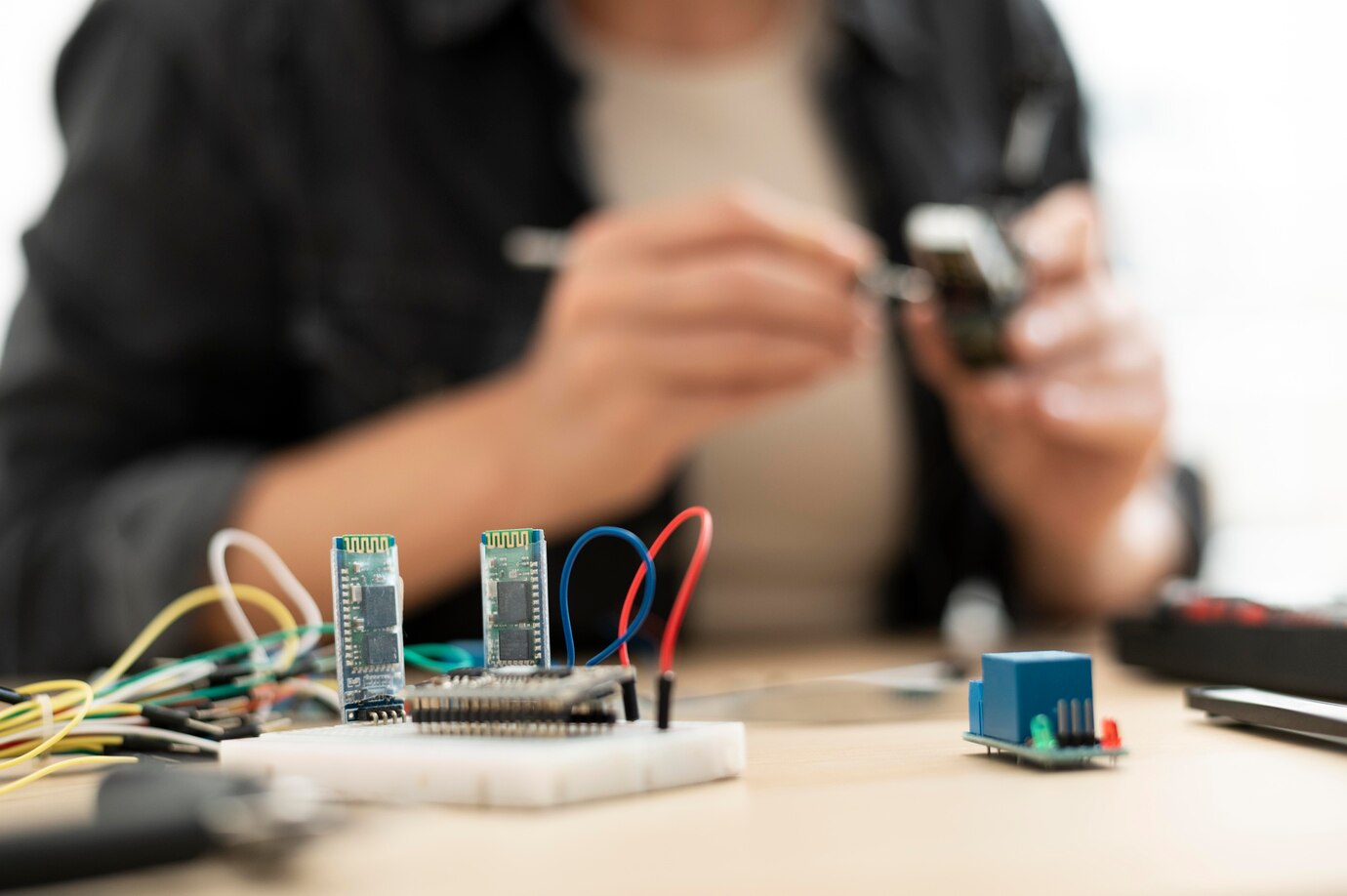
Printed electronics is an intriguing new area that has emerged in the dynamic world of electronics as a result of the merging of technology and flexibility. One of the many potential uses for this state-of-the-art manufacturing method is in wearable technology, but there are many more. It includes making electrical devices on flexible substrates. This article takes a deep dive into printed electronics, discussing how it is made and how it has affected the evolution of wearable technology.
First Principles of Printed Circuits
The use of silicon and other hard materials in traditional electronics production makes for less flexible and often larger gadgets. Conversely, printed electronics make use of novel production methods and materials to print electrical components onto malleable substrates like paper, plastic, or even fabrics. This paves the way for novel approaches to the creation of flexible, stretchy, and lightweight electronics.
1. When it comes to printed electronics, inkjet printing is a crucial method. The procedure involves depositing conductive inks onto a flexible substrate in a manner similar to that of a conventional inkjet printer onto paper. To facilitate the fabrication of circuits and components, these inks often include conductive elements, such as silver nanoparticles.
2. Screen printing is a technique that has been modified for use in the production of electronic components. In this process, conductive inks are deposited onto a substrate using a stencil. This method is both economical and well-suited for industrial-scale manufacturing.
3. The third method is flexography, which is often used in printing. It involves transferring conductive inks onto the substrate using a flexible relief plate. For rapid and massive manufacturing, this approach works well.
4. Gravure Printing: A cylinder is used in gravure printing to convey an image. The cylinder is coated with conductive ink and then pushed into a flexible substrate. The accuracy and superiority of the outcomes are hallmarks of this procedure.
The Era of Wearable Technology
A new era in wearable device design and usefulness has opened up because to the convergence of printed electronics with wearable technologies. When it comes to wearable technology, the need for flexibility and comfort makes traditional stiff circuits unfeasible. The development of smart textiles is made possible by printed electronics, which integrate electrical components into fabrics in a seamless manner.
1. Rollable and flexible displays that can fit the shape of garments have been developed thanks to printed electronics. As a result, novel wearables including smart apparel and accessories with screens for real-time data have emerged.
2. Wearable Health Monitoring Devices: The adaptability of printed electronics makes them ideal for a wide variety of wearable health monitoring devices, including smartwatches and patches. These monitor vital signs and provide useful health information while being pleasantly worn for long periods of time
3. Textile Integration: Intelligent fabrics may be made possible by printing electrical components directly onto textiles. Wearable technology that improves form and function includes sensors, heating components, and lights.
Positives and Negatives Advantages:
The use of printed electronics has made it possible to design electrical devices that are both flexible and stretchy. Efficiency: When it comes to mass manufacturing, printing might be a more economical option.
Personalization: Designers may make electrical components with whatever form they choose, so they can meet the needs of any project.
Challenges:
How long something lasts: Particularly in uses involving frequent bending or stretching, it is difficult to guarantee that printed electronics on flexible substrates will last.
Choosing the Right Materials: If you want your product to work as expected and last as long as possible, you need to use conductive inks and substrates.
Printed electronics continue to face the problem of scaling up production without sacrificing quality or consistency.
Looking Ahead: The Scene
Printed electronics have had far-reaching effects in many fields, including healthcare, the automobile industry, and wearable technology in particular. With the ongoing research and development, this revolutionary manufacturing process will be able to overcome present hurdles and uncover even greater potential. The future seems bright with the prospect of wearable technology expanding into new territories, the gradual blurring of boundaries between fabrics and electronics, and the generalization of these trends into our daily life.